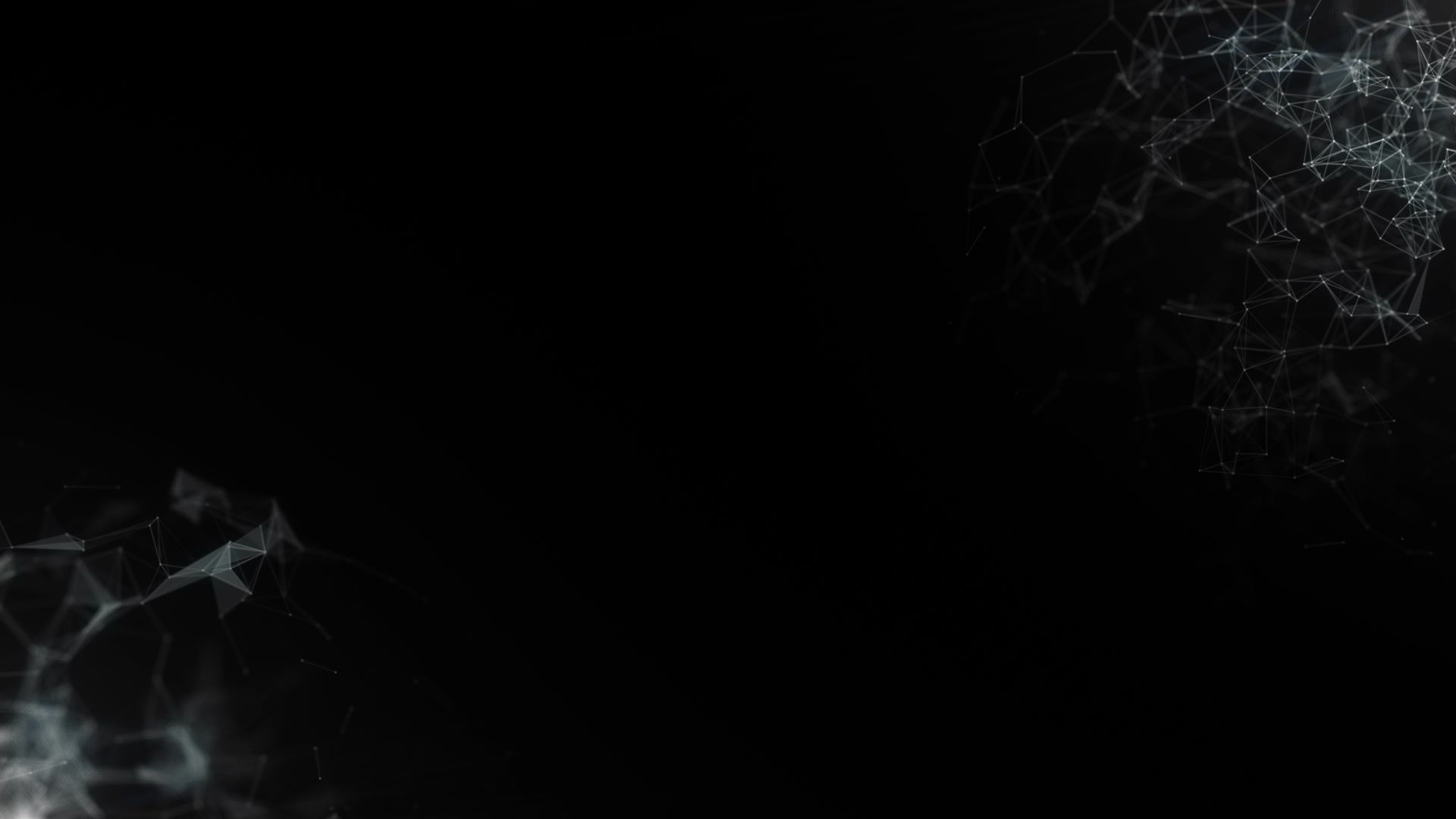
CoOp Villages.us
Back to Trades Area
Construction Flow
Pre-Construction Construction Phase Construction Techniques
Pre-Construction Phase
1. Have basic prints reviewed by an architect.
Incorporate suggestions into other designs
Finalize prints.
2. Secure General Contractor, Master Electrician and Master Plumber
If necessary, train persons in the above fields to obtain licenses to work under.
3. Purchase hand held navigational equipment and perform civil engineering surveys
ourselves to produce topographical maps for internal use only.
4. Lay out construction sites and roads on maps. Layout on-site.
5. Begin land clearing.
6. Install Basic Infrastructure:
-
-
Construct Roads
-
Order electric power mains
-
Install water wells
-
Install central septic tanks
-
Install construction shack with phone service
-
7. Construct or secure warehouse for bulk purchases.
Construction Phase, per Cluster Back to Top
A. Construct cluster garage, campground, gazebo, bathrooms (in place of washroom),
meeting room, temporary construction trailers.
B. Pour slabs. Install power poles where necessary
C. Frame walls and joists, pre-wire panels.
This can be done inside garage during extreme weather.
D. Assemble walls; install trusses and/or roof system,
E. Complete wiring, plumbing
F. Complete exterior, interior. Finish floors
G. Wire for phones/cable/computer
H. After wall sections for cluster are finished, convert garage to cabinet maker’s shop
and begin cabinets and built-ins.
I. After first few buildings are completed, make “jigs” where possible for
standardization and write training and procedure manuals for incoming
residents helping in construction.
J. Move campsite, construction trailers, construction office to next cluster.
K. Complete washroom.
L. Upon completion of third cluster, construct dining hall.
Construction Techniques
The Trades buildings might use the following construction methods:
Framing: Framing would be with 2” X 6” lumber. The building codes allows for 2 x 6’s to be on 24” centers, however we plan to use 16” centers to give the buildings more strength and a longer life.
Insulation: 6” thick walls allows for more insulation increasing the R value to near R -30.
Wall Surfaces: Internal would be sheetrock and external would be 4’ x 8’ hardy boards, which are cement and fiber panels with a 50 year life expectancy.
These boards are insect resistant as well as fire proof.
Roof System: Trusses would be manufactured on site. The roof would be heavy gauge white metal which should reflect 80% of the sunlight making the attic temperature equal to the outside temperature. This will save 25% on air conditioning costs. The metal would be fastened to 2” x 4’ purlins negating the need for plywood decking.
Ceiling System: The ceilings would be prepainted Styrofoam insulated panels (SIPs) 2’ wide x 12’ long which would be inserted between each roof truss.
This should yield an R-30 insulation value plus a finished ceiling in 2 hours.
Note: All of the above methods are such that novice builders can complete them with minimum supervision.